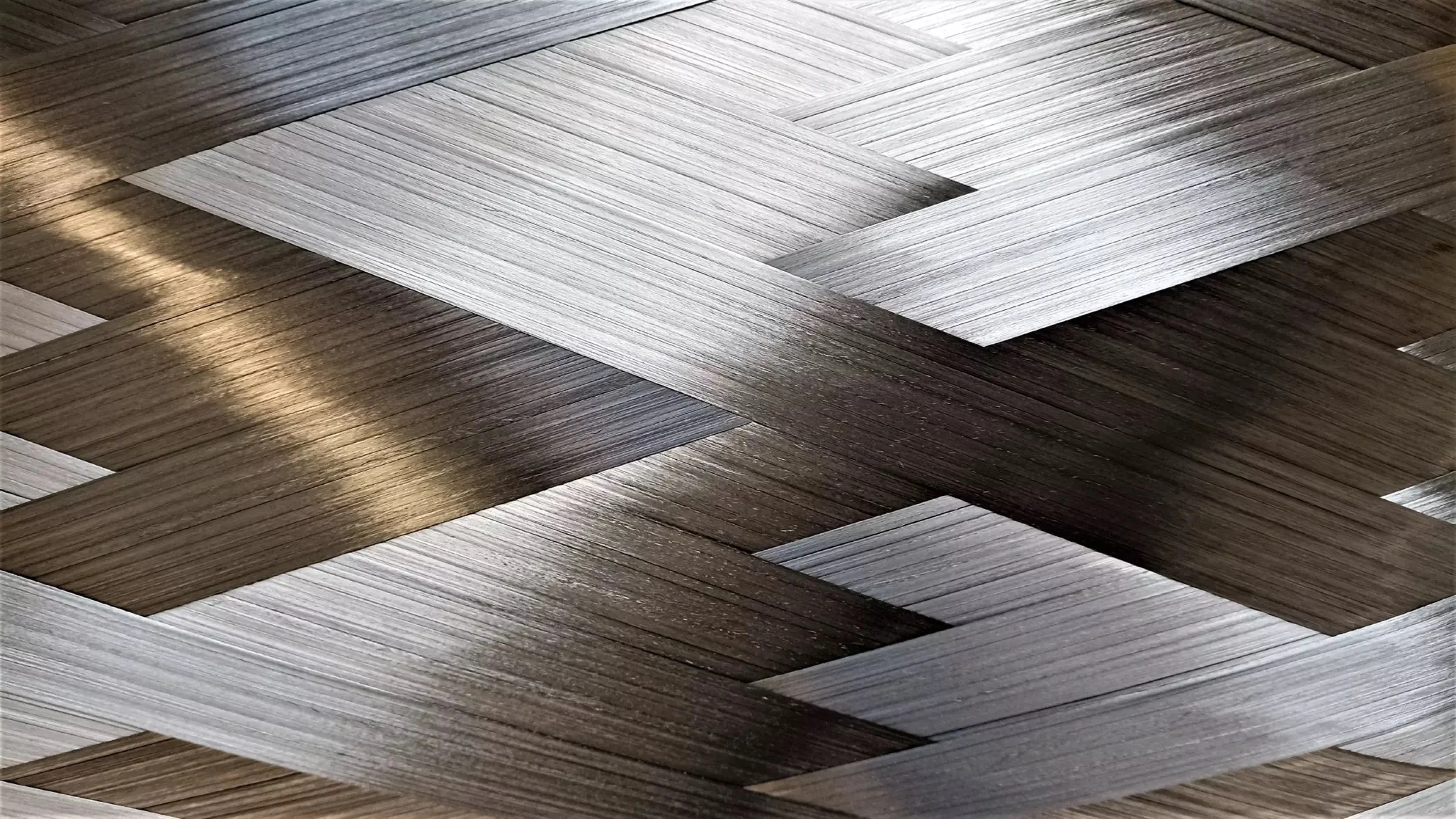
Composite Pressure Vessels
Composite Pressure Vessels
Composite pressure vessels are constructed from high-strength fibers, including but not limited to carbon, fiberglass, and aramid, which offer exceptional strength-to-weight ratios and corrosion resistance. Composite pressure vessels are a vital component in the storage and transportation of hydrogen. TANIQ has experience with the design and development of a large variety of Type III and Type IV composite pressure vessels.
Design of Type III and Type IV composite pressure vessels
We specialize in designing and developing Type III vessels (metallic liner, overwrapped with high-strength fibers) and Type IV vessels (plastic liner, overwrapped with high-strength fibers).
TYPE III composite pressure vessels
Our Type III tanks are designed with a metallic liner, which are then overwrapped with high-strength (carbon) fibre and epoxy, in precise patterns, using a filament winding machine. The fiber paths and patterns are designed using TaniqWind Pro software. With the FEA Toolbox high-fidelity, the data of the construction can be exported to FEA software (Abaqus, HyperWorks) for analysis and optimization.
Type III Composite Pressure Vessel design and FE modeling performed for Dawn Aerospace. Manufactured by Dawn Aerospace. Credit: Dawn Aerospace
TYPE IV composite pressure vessels
Our design of Type IV tanks incorporates a plastic liner with metal boss parts. TANIQ has developed these tanks based on ‘wet’ winding, pre-preg winding, dry winding, and laser-assisted thermoplastic tape winding. TANIQ has used different design strategies and FE modeling approaches for the different material/process combinations.
TANIQ had designed and developed Type IV composite pressure vessels using various liners and fiber types. TANIQ has experience with dry winding, wet winding, thermoset pre-pregs, and thermoplastic tapes.
Type IV Composite Pressure Vessel design, FE modeling and manufacturing together with Fraunhofer IPT using their laser-assisted tape winding head. Credit: Fraunhofer IPT (Germany).
Filament winding and tape placement
We design and produce Type III and Type IV composite pressure vessels based on various production techniques:
‘Wet’ filament winding:
The fibers are impregnated with an epoxy resin system during the process known as 'wet' filament winding. After winding, heat is applied to cure and consolidate the layers, forming a solid composite structure.
Pre-preg Winding:
In this process, the fibers are pre-impregnated with a thermoset resin, known as 'pre-preg' material. The dry pre-preg material is then wound onto a mandrel. After winding, heat is applied to cure and consolidate the layers, forming a solid composite structure.
Dry Winding:
In dry winding, fibers are wound onto a mandrel without using a resin or thermoplastic system. The resulting dry wound structure is covered with a protective coating.
Thermoplastic Tape Winding/Placement:
This method uses a heat source for in-situ consolidation. Thermoplastic tapes are wound around a mandrel using a contact roller, and heat and pressure are applied directly on the nip-point to melt and consolidate the layers, forming a solid composite structure.
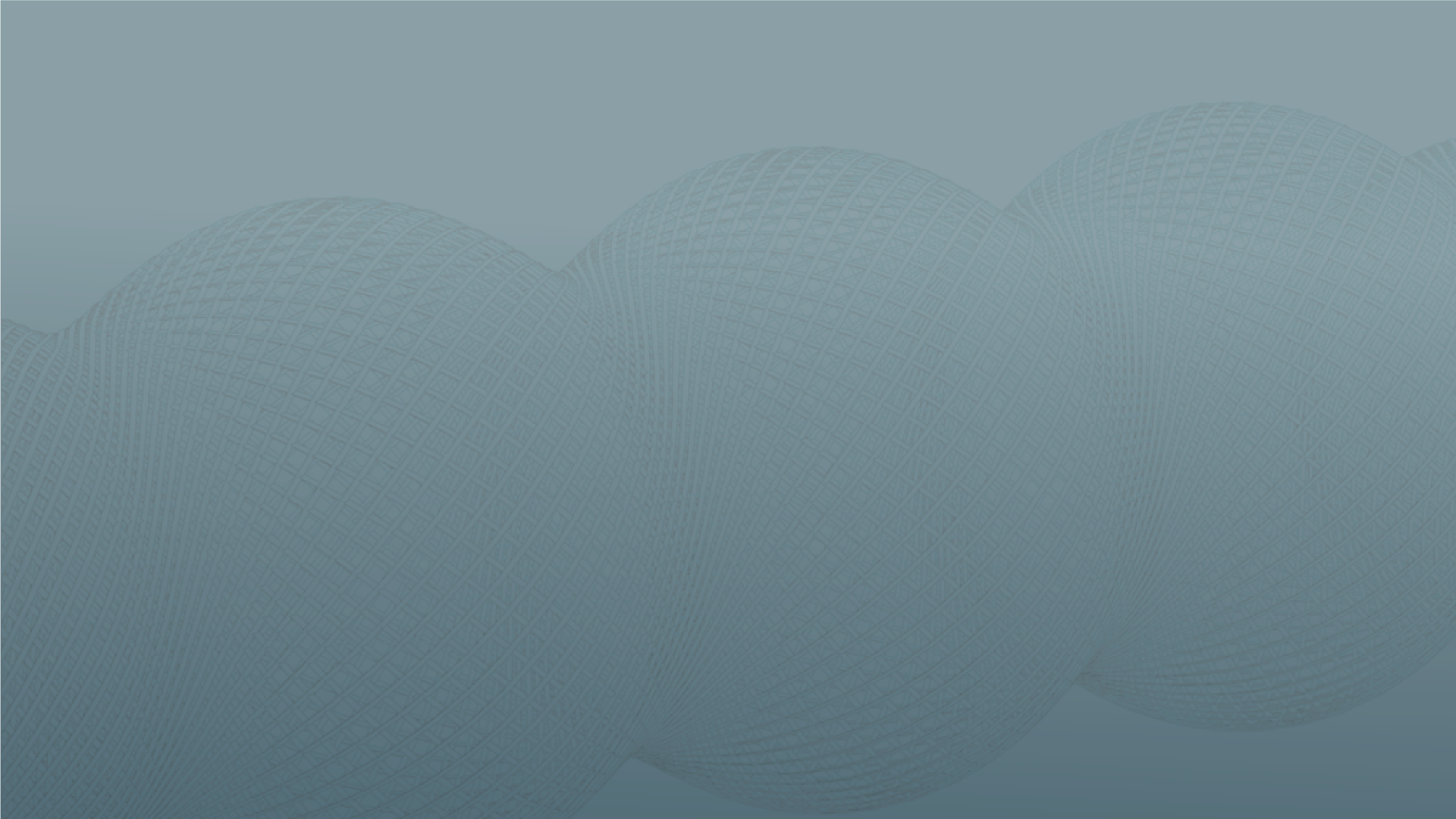