Scorpo TAURUS
Automated production of large hoses
After successful development of Scorpo VIRGO Robotics for medium size products, TANIQ has now developed Scorpo TAURUS Robotics for large diameter (0.4m -2m) hoses up to 12m long (Customisable according to customer's requirements). The developed set-up is not a conventional automation solution to replace the current manual production steps, but a new technology to optimize the hose reinforcement construction in combination with automated production. Optimisation of the reinforcement construction include topics such as continuous wound reinforcement layers, multiple- layer optimization and integrally wound metal couplings. These optimisations can only be implemented in production using accurate robotics.
Scorpo Taurus Robotics for large size products
Research and developments has resulted in a reliable automation solution for reinforced rubber hoses. A large variation of hoses (e.g. Dredging, Mining, Slurry, Material handling and Offshore) can be manufactured with the automated setup including placement of rubber, reinforcement material and wrapping tape. In addition to straight hoses, more complex products can be automated such as conical sections and convoluted hoses.
Integrated couplings
TANIQ's extensive experience in mandrel and product prototyping has lead to the development of integrated flanges and couplings. By integrally winding over the metal couplings, an extremely durable and rigged construction is created. Due to the cord structure and winding paths, the cords will exert extreme clamping-force on the metal coupling under any force equilibrium. As a result, an extremely durable product construction is created. The integral winding processes enable a continues material placement process, suitable for automation. As a result, TANIQ's Scorpo Taurus system ensures fast production and better performing hoses.
Customised automation of large hoses using Scorpo Robotics
The large Scorpo Robotics system for hoses relies on a combination of specially developed automation components. Like conventional production lathes, the mandrel is rotated on a powerful external axis. This axis can be modified to specification with customisation options like, e.g., servo power, mandrel support, mandrel connection to drive shafts, variable mandrel length support, and others. A Robotic arm on a parallel track (to the mandrel) is used to accurately place the materials. This robotic arm enables high speed and accurate placement. Moreover, it provides the required flexibility to manufacture a wide range of hoses on a single Scorpo Robotics cell.
The reinforcement cord, rubber and tape is supplied and placed with different tools that the robot arm picks-up automatically from a special tool station. Rubber and tape is supplied from spools, that are placed in the tools themselves. However, the cords are supplied by a specially developed tensioner that is placed on the track and moves simultaneously with the robotic arm. Using these tools, tensioner and winding principles, accurate and fast automated material placement is possible.
TANIQ's unique technology and link between the design software, FEA and robotic systems ensure that the actual products are identical to the designed product. The use of optimisation algorithms and multi-layer optimisation in the design software ensures that an optimum reinforcement structure of cords is used. The software calculates the correct reinforcement distribution to ensure an even load over multiple reinforcement layers is achieved. Adhesion research ensures that, in addition to an optimum reinforcement (with significant costs savings), actual product performance is exactly as designed with minimal performance degradation.
Learn more about the customisation possibilities of the robotic setups and winding principles of the materials.
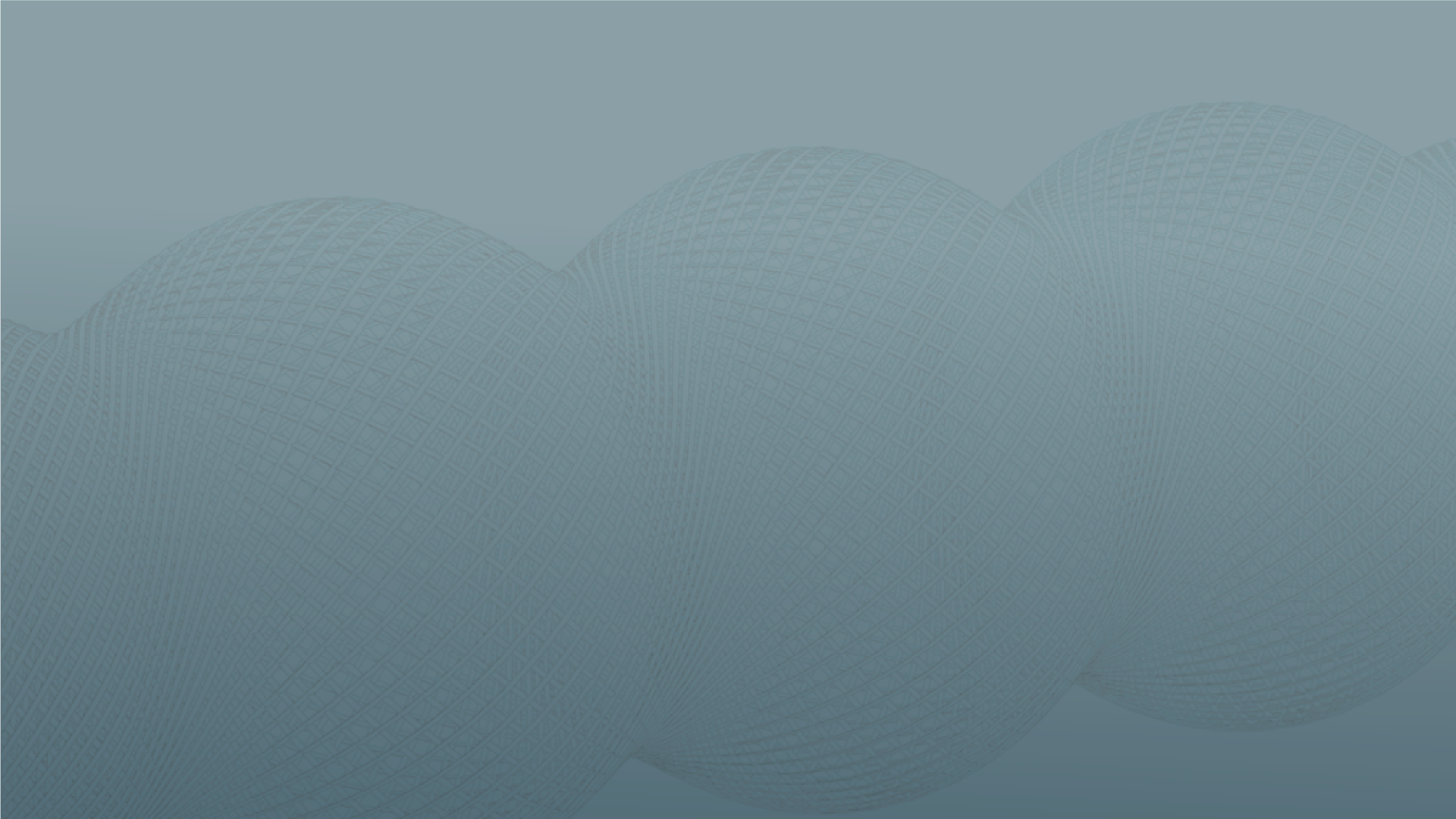