Scorpo VIRGO
Automated production of medium size products
To automate the production of reinforced rubber products of medium product size, TANIQ has developed the Scorpo Virgo. The Scorpo Virgo is suitable to manufacture products up to approximately 3000 mm length and 1500 mm diameter. The Scorpo Virgo is used for manufacturing of pipe-plugs, expansion joints and lifting bags, and is also suitable for products of comparable dimensions such as inflatable packers, pinch valve sleeves, air-springs and more. The system has been designed to be customised and optimised per customer. If customisation is required and to what degree customisation is required depends on the customers situation, for example, the product types, size range, design and facility.
Scorpo Robotics for medium size products
Research and developments has resulted in a reliable automation solution for reinforced rubber products. A large variation of products can be manufactured with the automated setup including placement of rubber, reinforcement material and wrapping tape. The system makes it even possible to manufacture multiple different product types and sizes on one and the same setup. For example, TANIQ's robotic testing facility normally houses two medium size robotic setups for research, development, prototyping and testing. The systems allow TANIQ to prototype al the mentioned products on both setups.
Customised automation of large hoses using Scorpo™ Robotics
The medium sized Scorpo Robotics system, known as Virgo , relies on a combination of specially developed automation components. Like conventional production lathes, the mandrel is rotated on an external axis. This axis can be modified to specification with customisation options like, e.g., servo power, mandrel support, mandrel quick-connectors, variable mandrel length support, and others.
A robotic arm next to the rotating axis is used to accurately place the materials. This robotic arm enables high speed and accurate placement. The use of a robotic arm is the key factor that enables the flexibility to quickly change product types and sizes. A industrial 6-axis robotic arm provides a wide reach area and all the degrees of freedom required. The specific type and weight rating of the robotic arm can be modified to facilitate the customer's requirements.
Using automated material winding tools; a specially developed cord tensioner; and TANIQ's winding principles, accurate and fast automated material placement is possible. The reinforcement cord, rubber strip and tape are accurately placed with these different tools. The robot arm has been programmed to automatically picks-up the tools from a special tool station. The rubber strip material and tape is supplied from spools, that are placed in the tools themselves. However, the cords are supplied by a specially developed tensioner that is placed on the side of the robot cell. TANIQ continuously develops these robotic tools and tensioners. Thereby, providing the possibility to customise the tools or develop completely new tools if required.
TANIQ's unique technology and link between the design software, FEA and robotic systems ensure that the actual products are identical to the designed product. The use of optimisation algorithms and multi-layer optimisation in the design software ensures that an optimum reinforcement structure of cords is used.
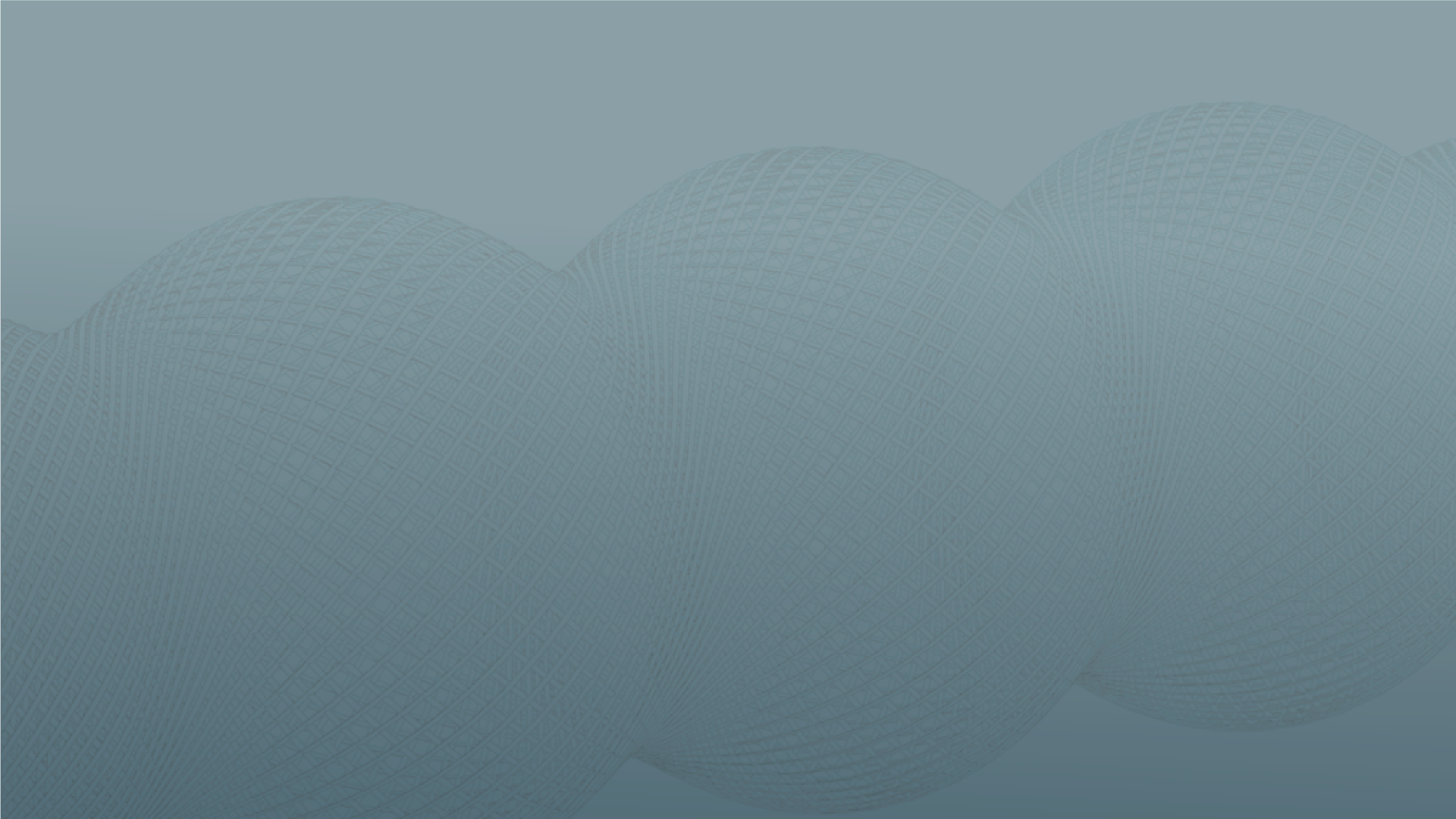