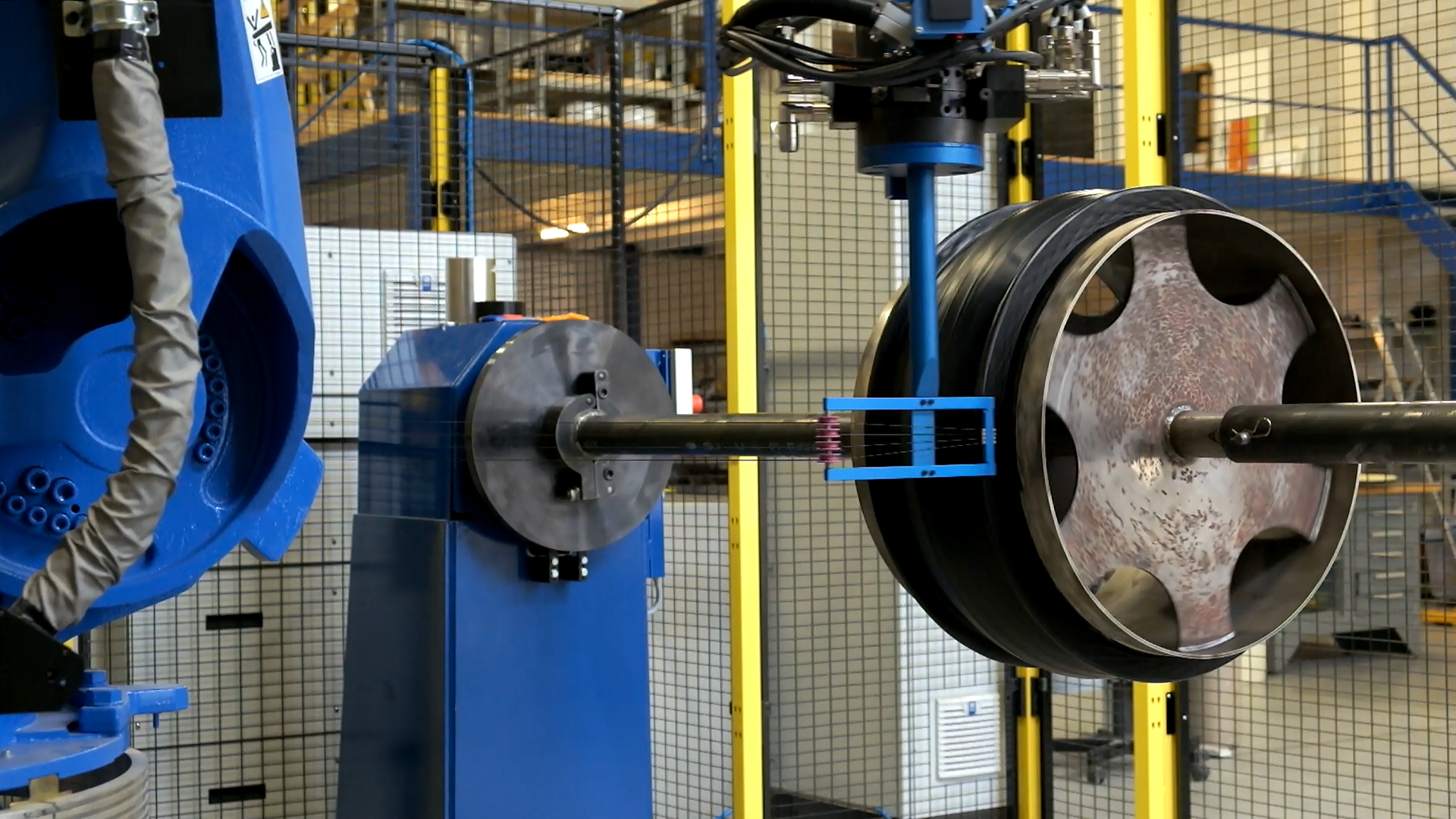
Scorpo FAQs
FAQ about TANIQ's Scorpo™ setups for reinforced rubber products
Robotic automation with the exact geometry of the designed products makes production faster, more accurate and more consistent. Resulting in a significant reduction of labour and production cost as well as time. Robotic placement of all the material layers creates consistency in the form of repeatability and reliability of performance (and looks). Moreover, production is less dependent on training and skill of employees. The system can be operated by a single operator and provides a user friendly step-by-step interface. The basics and Frequently Asked Questions about the automation systems provide an introduction to Scorpo™ Robotics.
Custom automation solution platform
-
Scorpo™ Robotics is the trade name for TANIQ's robotic production equipment for automated placement of rubber, reinforcement and (nylon) pressure tape.
-
The main components are indicated in the system overview illustration. The exact configuration and dimensions of the set-up depend on the specifications of the product(s) which will be manufactured on the set-up. All setups consists of 8 main components. A flexible industrial robotic arm forms the core of the set-up (1) and places the material with the help of tools. The product is manufactured on an inner mandrel that is rotated with the external axis/mandrel rotator (2). The simultaneous and interconnected movement of the robot arm and mandrel rotator is controlled with the robotic controller unit (3). The set-up is surrounded by an intelligent safety fence (4) with an electronic door connection to the robotic controller unit.
Material placement is done with the various specially developed tools that ensure placement with consistent tension and pressure. The set-up includes a rubber winding tool (5) for placing a wide variety of rubber strip types on the mandrel. Fibre reinforcement placement on the optimum position is possible with the fibre winding tool (6) and specially developed fibre tensioner (7). Lastly, a pressure tape tool is included (8).
For the manufacturing of large size products such as dredging hoses the robot moves on a rail parallel to the mandrel rotator to enable product lengths up to 12m.
-
TANIQ's design software is incorporated in your turnkey production solution. TANIQ will develop customized design software for you, which enables you to make new designs yourself. You can easily make new designs by changing the parameters such as dimensions (length, diameter, etc.), pressure, and materials. After making a new design you can directly update it your robot for production. An important advantage is that your design and production know-how will be embedded in your software which makes you less dependent on skilled workers and their training. More information on the software can be found under Design Software.
-
The dimensions of the Scorpo™ set-up are based on the desired product dimension by our customers. Each robot has its maximum reach which allows to manufacture up to certain dimensions. This work range can be extended. For example by placing the robot on an elevated base or rail. The table gives an indication of product dimensions for medium size products and for large size products.
-
The Scorpo™ Robotics set-up can be designed to make small turbo hose up to large diameter dredge hoses. An overview of products can be found under Applications. Set-up customisation ensures that the robot is applicable to a wide range of products. Special development and continuous R&D constantly increase the possibilities of Scorpo™ Robotics.
-
A Scorpo™ set-up can be operated by a single operator. The operator will be guided through the production process following a step-by-step production manual on the touchscreen (HMI). On this touchscreen an instruction line will appear for every task the operator has to execute. Thanks to these step-by-step instructions TANIQ can train an operator to manufacture products on the robot within 2-3 days.
While the production is highly automated the operator will execute tasks like placing/removing the product mandrel, starting the production program, attaching material at the begin/end of a winding procedure and replacing empty material spools. When the robot is winding the materials the operator has time to prepare or finish another product, or do other tasks around the set-up. Note: For the placement and removal of large product mandrels it can be necessary to have temporarily assistance of a co-worker.
-
The maximum winding speeds are determined by the maximum robot acceleration and the maximum turning speed of the mandrel. The latter is limited by maximum mandrel weight and moment of inertia.
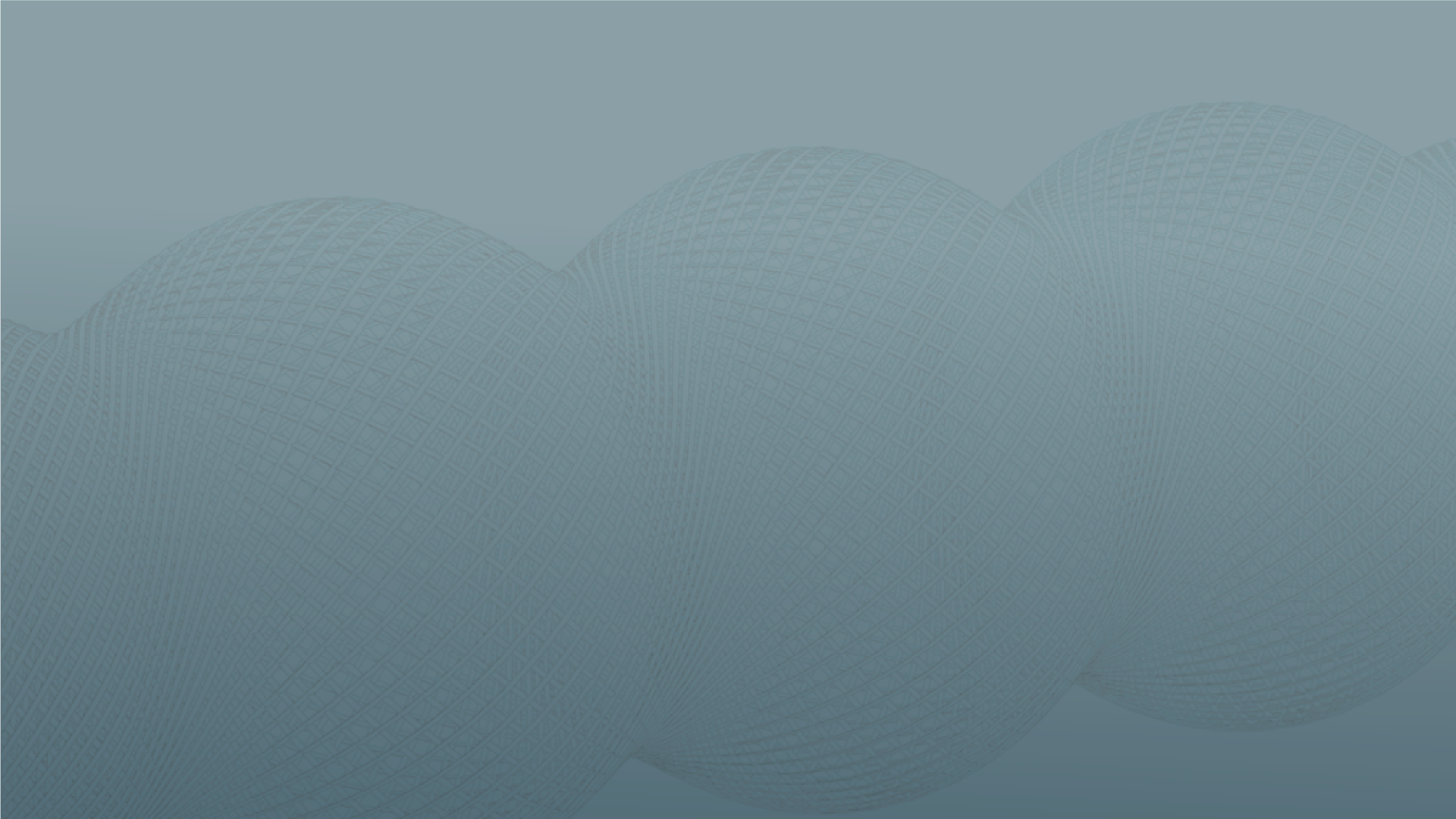