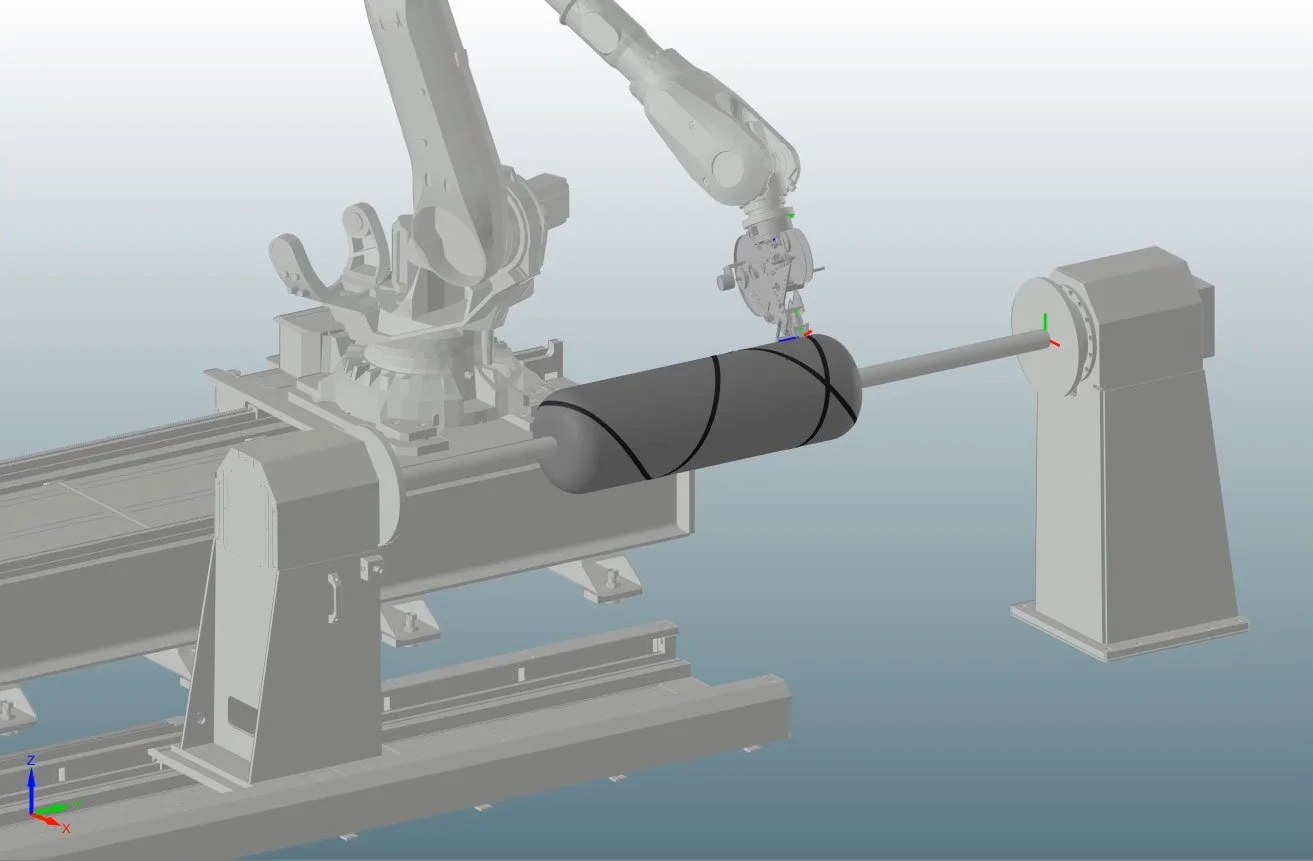
TaniqWind Pro - Filament Winding Software
TaniqWind Pro - powerful CAD/CAM software for composites
TaniqWind Pro is a powerful software for design and manufacturing of composite parts such as pipes and pressure vessels. TaniqWind pro can be used for (wet) filament winding, towpreg winding and winding/placement of thermoplastic tapes. TaniqWind is the result of 14 years of development by a team of winding experts, and it is the most actively developed software on the market resulting in continuous improvements and added functionality for the users.
Demonstration: Highlighted Features
In the following video, we visualize the highlighted features that come with TaniqWind Pro
Composite Design
TaniqWind Pro is developed to provide engineers with the best possible software for designing composite pressure vessels. The software has advanced functionalities for designing fiber paths and patterns, providing insight in all design criteria (fiber angle, friction, coverage, dwell) in a single panel. The software contains an advanced build-up toolbox providing accurate build-up prediction for both fiber and tape layers, including extended options for smoothing. As a result, the composite design made in TaniqWind Pro gives the user a realistic representation of the actual composite structure, forming the bases for creating high fidelity FE Models, and generating of the Robotic or CNC winding programs.
FE Modeling: Analysis and Optimization
The composite design made in TaniqWind Pro can be analyzed and optimized using finite element analysis (FEA) software. The software has integrated FEA export functionalities for HyperWorks Multi-Scale Modeling. In July 2023 a new Abaqus export functionality will be released, supporting all conventional data formats for modeling of shell, 2D axisymmetric and full 3D modeling. Additionally, unique export formats can be developed on request, such as the special shell element required for Multi-Scale Modeling in HyperWorks.
Robotic and CNC winding programs
TaniqWind Pro has powerful tools for generating production programs for both Robotic and CNC winding systems. The generic CNC post-processor allows the user to configurate their winding machine by specifying each individual axis of the equipment. Where other winding software on the market are controlling the robot through the CNC post-processor, TaniqWind Pro has a separate post-processor for robotic winding, taking maximum advantage of the movement capabilities of the robot.
Feature Overview
Basic Features:
Mandrel generation (continuous profile)
Mandrel data import feature (incl. DXF)
Pipes, Pressure Vessels and axis symmetrical mandrel geometries
Winding path & pattern generator
Geodesic and non-geodesic winding paths
Circumferential (hoop) winding
Helical winding
Transition layer winding
Coverage path
Segmented path option for designing advanced winding paths
Winding path and pattern simulation
FEA export functionality (shell, 2D axisymmetric, full 3D)
Generic CNC post-processor
Robotic CNC post-processor
Machine Program editor (e.g. Syntax, Declarations, etc.)
Customizable process settings panel (e.g. variable winding tension)
Highlighted features:
Highlighted features
Continuous Mandrel Profile Description
Instead of discretizing the mandrel surface into individual sections, TaniqWind uses a novel approach providing a continuous representation of the surface using an analytical model. This improved profile definition increases the accuracy of the winding paths, leading to improved product quality and smoother machine movements.
Improved profile description as continuous analytical surface
Increased accuracy of winding path calculations
More accurate and reliable FE results
Smoother machine movements
2. Coverage path algorithm
The coverage path algorithm automatically searches for a tape path corresponding to the requested coverage. This is achieved by automatically changing several parameters within a given bandwidth such as i) winding angle, ii) polar opening, iii) friction and iv) dwell. This functionality is especially useful for designing pressure vessels whereby a 200% coverage per layer is required, without having gaps or overlap between adjacent tapes.
Software automatically searches for a tape path trajectory for the requested coverage within specified bandwidth of the following criteria:
Angle
Polar opening
Friction
Dwell
3. Adjustable start-winding position
TaniqWind has a unique function for shifting the start-winding-position to any location on the profile. Instead of having a fixed start-stop position, this position can be defined separately for each layer. This allows to start a helical layer on any desired position on the cylinder or dome sections. Spreading of the start-stop positions prevents local build-up and stress concentrations in the composite structure.
Start winding at any desired location along the profile
Start-stop position are identical
4. Constant in-plane curvature paths
Besides friction, also constant in-plane curvature can be used to generate non-geodesic paths. The constant in-plane curvature functionality creates tape paths using the maximum allowable in-plane curvature as the criteria. This feature is especially useful for tape placement processes where path trajectories are not defined by friction but are restricted by the maximum allowable in-plane curvature of the tape.
Design winding paths based on in-planar curvature of the tape to prevent buckling
5. Build-up model for tapes
TANIQ has developed sophisticated mathematical models resulting in a powerful build-up prediction panel for filaments and tapes. In the panel, the calculated build-up profiles can easily be adjusted or smoothened. The improved build-up calculation provides accurate predictions of actual build-up behavior during manufacturing, drastically improving consistency between the Finite Element Model and the final product.
Advanced mathematical models to represent the build-up behavior
Optimized for critical product regions such as domes and polar openings for pressure vessels
Build-up panel with options for ‘smoothing’
Accurate match of actual build-up behavior during manufacturing
High consistency between the design, FEA model and the final product
6. Finite Element Model Export
TaniqWind has an integrated functionality to export design data based on a unique shell model, supporting HyperWorks Multi-Scale modelling approach for COPVs. Due to the specific data structure developed in collaboration with Altair, unique details and information of the winding structure are included in the output towards Altair HyperWorks, resulting in more highly representative outcome.
Generate data file for FE models automatically
Unique structure and information included in export file
Resulting in a more representative models
In the coming months, the FEA export functionalities will be extended supporting shell, 2D axisymmetric and full 3D in Abaqus.
7. Powerful Post-processor
Within TaniqWind users can define their Robotic or CNC winding machine and create a post-processor. In the post-processor panel, the user can customize the machine program and production procedure, having full access to the software computed trajectory (e.g. machine positions, orientations), providing users with a powerful tool for creating customized production programs.
Make post-processor for your Robotic or CNC winding equipment
Maximum freedom for customizing your winding programs
8. Production parameter integration
In the production settings panel, the user can define production parameters such as tape tension or laser power and set variable values for these production parameters per layer, and even per different section in the profile. Examples: varying the winding tension between hoop and helical layers or varying laser power for different sections within a layer.
Add and definde process control parameters
Set variable values for process parameters for different profile sections
9. Robotic winding fully integrated
TaniqWind was developed in 2007 for Robotic Winding and has a dedicated robotic post-processor taking full advantage of all motion and control capabilities (instead of CNC movements being converted to robot movements). Some options within the software are defining a robot-held mandrel with stationary winding eye, defining additional twist/yaw axis on the tool, and checking for reachability and singularity & collision detection.
Dedicated post-processor for robotic winding
Utilizing all motion capabilities of the robot
Including reachability checks, and singularity & collision detection
10. Software as a Service (SaaS)
TaniqWind is offered on a subscription basis, whereby the user can select the package (Lite, Extended or Full) and options that best fits their needs. The subscription model provides greater flexibility, scalability and cost-effectiveness. The TaniqWind subscription includes automatic updates and maintenance, providing users with access to the latest updates and improvements without additional costs or efforts.
Subscription based model offering flexibility, scalability and cost-effectiveness
Including automatic updates & maintenance
Watch a tutorial of a full workflow on TaniqWind Pro
More information
Our winding experts are happy to explain you more about the functionality of the software. Feel free to contact us for more information or requesting a software demo.
